How to Reduce the Defects in Plastic Mold Processing?
Even if is very professional and have rich experience in plastic mold processing, also can't guarantee the production of plastic mold is one hundred percent qualified, more or less has some processing defects. But these defects can be controlled and life of the mold can be improved.
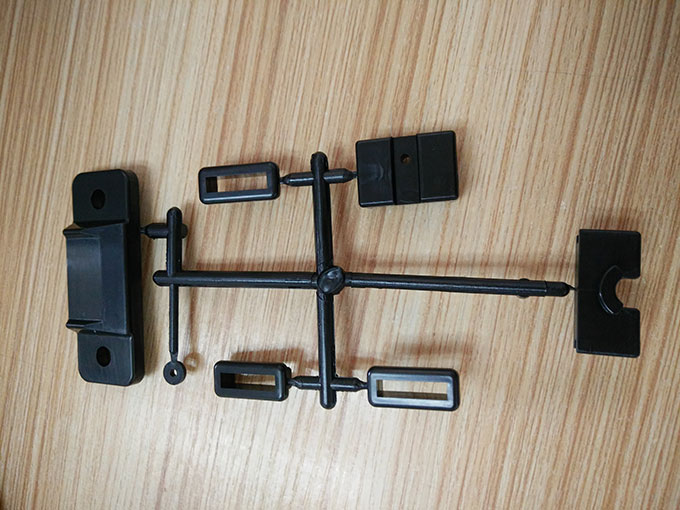
Below is the methods of reducing the defects in plastic molding processing:
Reasonable use of cooling lubricant, playing the role of cooling, washing and lubrication, thus to make the grinding heat is in allowable limitation, avoiding workpiece thermal deformation. Improving cooling conditions during grinding, such as the use of oil sands wheel or internal cooling wheel. The cutting fluid is leaded into the center of the grinding wheel, and it can directly enter into the grinding zone to play an effective cooling effect to prevent the surface burns of the workpiece.
After heat treatment, the quenching stress reduced to a minimum. The structure of quenching stress and network carbonization structure produce phase transitions under the grinding force, easily to make workpiece crack. In order to eliminate the residual stresses of grinding, low temperature aging should be done after grinding to improve toughness.
To eliminate the grinding stress, the mold can be soaked for 1.5min in the 260-315 degree celsius salt bath, and then cooled in 30 degree celsius oil, so that the hardness can be reduced by 1HRC and the residual stress decreased by 40%~65%.
For the size tolerance of precision grinding of precision molding is within 0.01 mm, should pay attention to the influence of environment temperature, requiring constant temperature grinding. From the calculation, it can be seen that the steel parts of 300mm long and the temperature difference of 3, the material has a change of 10.8 micrometre.(10.8=1.2*3*3,each 100mm deformation amount is 1.2 micrometre/celsius). The influence of this factor should be taken into consideration in all finishing processes.
Working with electrolytic grinding to improve the precision and surface quality of die. When electrolytic grinding,the grinding wheel removes the oxide film: Not the metal of grinding, the grinding force is small and the grinding heat is also small. There won't be the phenomenon such as burr, crack and burns, general the surface roughness can be better than Ra0.16 micrometre.In addition, the abrasion of the grinding wheel is small, such as grinding hard alloy. The abrasion of the silicon carbide wheel is about 400%~600 of the hard alloy weight. Using electrolytic grinding, the abrasion of grinding wheel is only 50%~100% of hard alloy grinding.
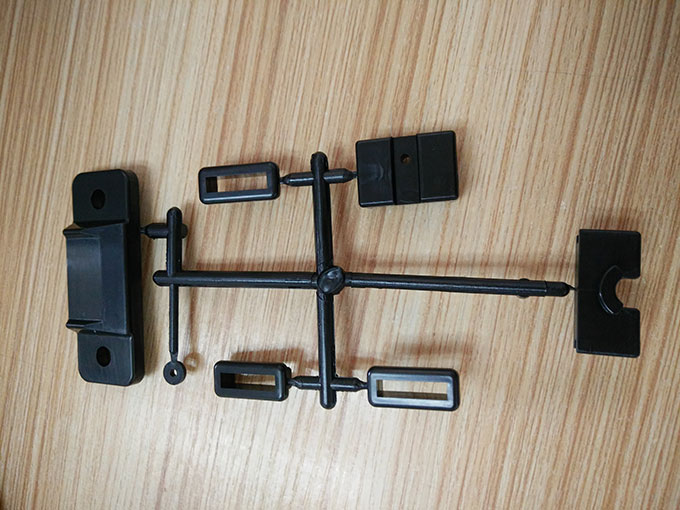
Below is the methods of reducing the defects in plastic molding processing: