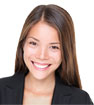
Mold Manufacturer China

Home » Basics
Usually one finished plastic product consists of more than one component plastic part. To save the mold cost, a family mold is required instead of making one mold for each part. A family mold is a multi-cavity injection mold in which each cavity forms a different part of the finished product.
There are many new inquiries coming in every single day, some of customer just provide very limited information, we can see a signal of no much intention to cooperate. On the other hand, we take serious for those inquiries that the information provided is very specific, and customer know exactly what they need. More detailed information, more proper solution.
When it comes to prototype, usually we use 3D printing or CNC machining to make it. A prototype making is an important step for verify the design, it can provide a proof of the feasibility for the part design, a physical sample for the mold design and injection molding. Most of designers would like to take this step before large amount investment/ before the project starts.
A mold with multi cavity can produce parts with higher efficiency; it is frequently applied to meet the high demand volume requirement. The number of the cavities and injection mold manufacture depends on both economical and technical factors, following factors needs to be considered to achieve the most proper mold cavity for your project.
Plastic injection molding is an important molding method for plastic products, which is widely used in mass production of plastic products with complex shapes and precise sizes. In the past years, we have been asked lots of questions about plastic injection mold except the tooling cost. Followings are some answers to the most frequently asked questions.
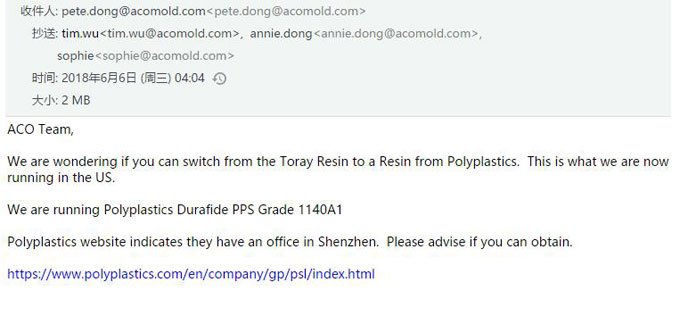
The purpose of plastic electroplating is to coat on the surface of the plastic with metal, which not only makes a better outlook, but also compensates the shortcomings of the plastic, imparts the properties of the metal, and fully utilizes the characteristics of the plastic and the metal. Today, a large number of plastic electroplating products have been applied to electronics, automobiles, household goods and other industries.
Prototype making is an importation step of the product design and processing injection mold, it provide an proof of the feasibility for the designing and a physic sample for the mold designing and injection mold manufacturing. So most of the designer would like to make a prototype to verify their design before the project starts.
Nylon is a crystalline plastic with a wide variety of varieties, reaching more than 130 varieties. Applied to injection molding are nylon 6, nylon 66, nylon 610, nylon 1010 and copolymerized nylon, super tough nylon, glass fiber reinforced nylon, mineral reinforced nylon and the like. In the world's plastics processing market, the most widely used in plastic molding is nylon 66.
The application fields of nylon 66 are generally in the fields of automobiles, electronic appliances, chemical equipment, machinery and the like. From the end use point of view, the nylon 66 consumed by the automotive industry took the first place, and the electronic appliances accounted for the second place. About 88% of nylon 66 is processed into various plastic products by injection molding, and about 12% of nylon 66 is processed into corresponding plastic products by extrusion, blow molding and other molding processes.
The application fields of nylon 66 are generally in the fields of automobiles, electronic appliances, chemical equipment, machinery and the like. From the end use point of view, the nylon 66 consumed by the automotive industry took the first place, and the electronic appliances accounted for the second place. About 88% of nylon 66 is processed into various plastic products by injection molding, and about 12% of nylon 66 is processed into corresponding plastic products by extrusion, blow molding and other molding processes.
Usually the new developed and designed products need to make prototypes. Rapid prototyping is the first step of verifying the feasibility and manufacturability of the product, is the most direct and effective way to find out the defects and disadvantages of the designed products, so as to improve until you can't find the deficiencies from prototypes. At this point, it is usually necessary to carry out low volume production to perform trial production to find out the shortage in the large volume injection molding, so as to improve. There is no 100% perfect product design, and sometimes the designed plastic products can't be normally used. Once there are defects in the large volume injection molding, the all injection molded parts will be scrap, which will waste manpower and material resources and time. The prototypes are generally a small number of samples, the prototype manufacturing cycle is short, and the human and material loss is low. Quickly find out the inadequacies of product design and improve it, and provide sufficient basis for batch injection molding.
Improper injection mold design often results in various defects of finished plastic products. Before modifying the injection mold, first do mold trial and evaluate, optimize the injection mold design and injection molding process parameters, usually can achieve twice the result with half the effort, while meeting the high quality requirements of large volume injection molding.
Guangdong
Guangdong is the most important plastic injection mold market in China now, and it is also Chinese largest plastic mold export and import province. More than 40% of the Chinese plastic injection molds are made in Guangdong. And the numerical control rate of and equipment performance of mold machining equipment, mold processing technology, production specialization level and standard level lead other provinces and cities in China.
Among the top 10 injection molding companies in China, there are five companies are from Guangdong. And the world's largest mold base supplier and Asia's largest injection molding manufacturer are in Guangdong.
With the further optimization of Guangdong's industrial structure, the development of many industries such as petrochemicals, automobiles, and high-tech has put forward higher requirements for injection mold manufacturing in Guangdong. In the next few years, injection mold manufacturing will become increasingly precision and high-end.
Guangdong is the most important plastic injection mold market in China now, and it is also Chinese largest plastic mold export and import province. More than 40% of the Chinese plastic injection molds are made in Guangdong. And the numerical control rate of and equipment performance of mold machining equipment, mold processing technology, production specialization level and standard level lead other provinces and cities in China.
Among the top 10 injection molding companies in China, there are five companies are from Guangdong. And the world's largest mold base supplier and Asia's largest injection molding manufacturer are in Guangdong.
With the further optimization of Guangdong's industrial structure, the development of many industries such as petrochemicals, automobiles, and high-tech has put forward higher requirements for injection mold manufacturing in Guangdong. In the next few years, injection mold manufacturing will become increasingly precision and high-end.