Low volume injection molding-3D printing
In the past, molds for injection molding were usually made of steel or aluminum, and were manufactured using reduced-material manufacturing techniques, such as CNC machine tools. But more and more companies have recently tried to use more advanced 3D printing processes to simplify the mold making process.
HASCO is Europe's leading molding services and injection mold making company and is considered to be the maker of European mold standards. The injection mold company recently developed a Quick-Change Mold System that allows injection molding manufacturers to quickly and efficiently replace molds to reduce the time and expense of resetting their machines. In particular, the use of 3D printers to print out the molds makes the whole process cheaper, allowing faster, cheaper prototyping, manufacturing samples, or cost-effective low volume injection molding.
As products get to market faster and produce less, customers are looking for solutions that enable them to be prototyped quickly, cost-effectively and efficiently. Compared to traditional metal or aluminum inserts, the new approach allows injection mold makers to achieve flexible and fast production and exchange of molds for greater efficiency and profitability. By combining HASCO's long-standing experience in traditional mold manufacturing with Stratasys' advanced technology in 3D printing and injection molds, this best-in-class technology is the future of prototyping and small-volume production.
The injection mold was printed using Objet500 Connex 3D printer, which uses the ultra-durable digital ABS material. The Objet500 Connex is not only one of the most advanced multi-material 3D printers on the market, but also a very fast printing machine. By using 3D printing instead of aluminum for milling, the injection mold making time is greatly reduced, and the prototype and mold can be adjusted quickly and economically. When combined with its K3500 quick-change mold system, 3D printing molds set a new low-cost benchmark for prototype and low-volume injection molding.
The speed of the whole process is amazing. With our Objet500 Connex 3D manufacturing system, we can make cavity parts for molding polymers in 6 hours, which previously required 24 hours. By standardizing Trial and testing of HASCO products and advanced Stratasys' 3D printing technology has proven that this innovative and fast technology can be applied in the injection molding process. For small batch prototypes produced using final product materials, quick change with 3D printed cavities Model is a fast and economical alternative to traditional methods.Welcome to ACO Mold injection molding manufacturer and contact us to get free quote.
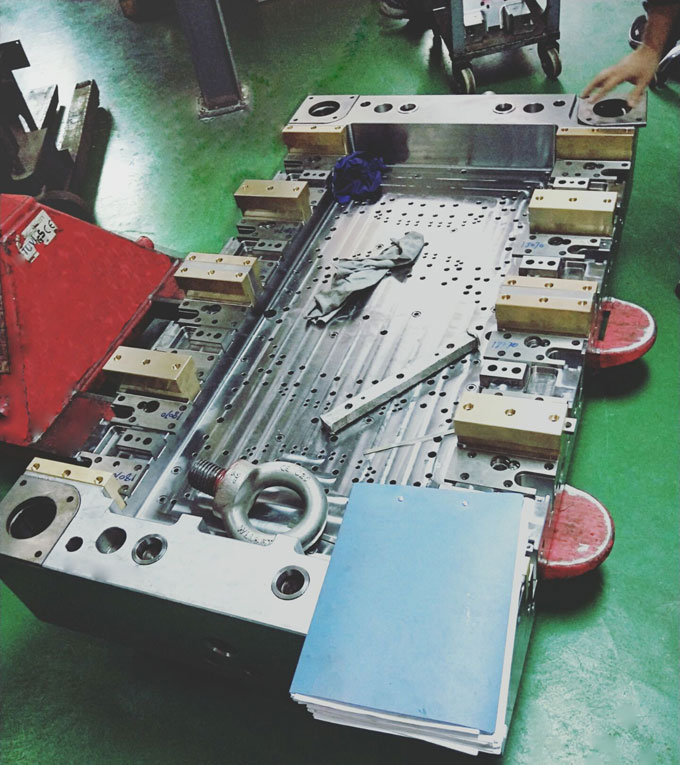
HASCO is Europe's leading molding services and injection mold making company and is considered to be the maker of European mold standards. The injection mold company recently developed a Quick-Change Mold System that allows injection molding manufacturers to quickly and efficiently replace molds to reduce the time and expense of resetting their machines. In particular, the use of 3D printers to print out the molds makes the whole process cheaper, allowing faster, cheaper prototyping, manufacturing samples, or cost-effective low volume injection molding.
As products get to market faster and produce less, customers are looking for solutions that enable them to be prototyped quickly, cost-effectively and efficiently. Compared to traditional metal or aluminum inserts, the new approach allows injection mold makers to achieve flexible and fast production and exchange of molds for greater efficiency and profitability. By combining HASCO's long-standing experience in traditional mold manufacturing with Stratasys' advanced technology in 3D printing and injection molds, this best-in-class technology is the future of prototyping and small-volume production.
The injection mold was printed using Objet500 Connex 3D printer, which uses the ultra-durable digital ABS material. The Objet500 Connex is not only one of the most advanced multi-material 3D printers on the market, but also a very fast printing machine. By using 3D printing instead of aluminum for milling, the injection mold making time is greatly reduced, and the prototype and mold can be adjusted quickly and economically. When combined with its K3500 quick-change mold system, 3D printing molds set a new low-cost benchmark for prototype and low-volume injection molding.
The speed of the whole process is amazing. With our Objet500 Connex 3D manufacturing system, we can make cavity parts for molding polymers in 6 hours, which previously required 24 hours. By standardizing Trial and testing of HASCO products and advanced Stratasys' 3D printing technology has proven that this innovative and fast technology can be applied in the injection molding process. For small batch prototypes produced using final product materials, quick change with 3D printed cavities Model is a fast and economical alternative to traditional methods.Welcome to ACO Mold injection molding manufacturer and contact us to get free quote.
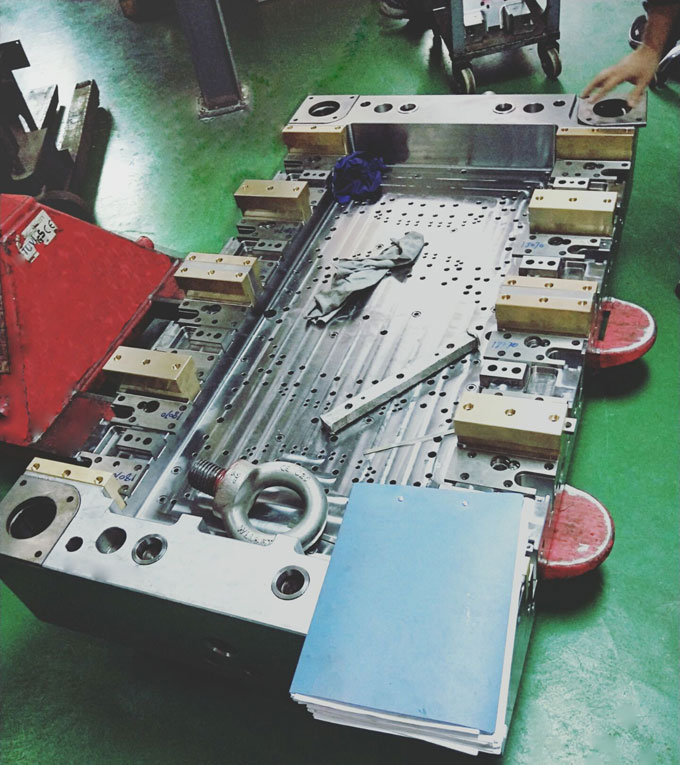