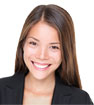
Mold Manufacturer China

It has been proven that electric injection molding machines are much better than hydraulics for many reasons such as, less power consumption, very quiet operation, no oil leaks, repeatability, independent drives (it is easy to achieve parallel movement of the injection molding machine), reliability, no linear transducers and ideal for clean rooms.
Most of the injection molding machine manufactures tend to use the same control panel for both hydraulics and electric but the way electrics control velocity to pressure and screw recovery are different to hydraulic injection molding machines, some machines have shown some issues due to this, also when using core pulls on electric injection molding machines it may be required to get a mobile hydraulic core pull unit as some tools have hydraulic core pulls.
Most of the injection molding machine manufactures tend to use the same control panel for both hydraulics and electric but the way electrics control velocity to pressure and screw recovery are different to hydraulic injection molding machines, some machines have shown some issues due to this, also when using core pulls on electric injection molding machines it may be required to get a mobile hydraulic core pull unit as some tools have hydraulic core pulls.
We all know that the skin layer in a molded part with PP is less crystalline than the core in a PP injection molded component. Could you please explain the mechanism behind why it happens? Is it due to the rapid cooling during the cooling cycle during injection molding which prevents the formation of crystalline phases? If there is some literature on the internet which explains the same I would like the links to the same.
The crystalizing of the material takes time and usually progress better at temperatures a bit higher than the injection mold surface temperature (actually in some cases you might gain cycle time by increasing injection mold temperature when running crystalline materials). Some companies make inductive heaters for the injection mold to increase the surface temperature to get close to the melt temperature to avoid or reduce the frozen layer. Then they apply a rapid cooling system with optimized cooling channel design and in some cases using an expanding gas for cooling.
The crystalizing of the material takes time and usually progress better at temperatures a bit higher than the injection mold surface temperature (actually in some cases you might gain cycle time by increasing injection mold temperature when running crystalline materials). Some companies make inductive heaters for the injection mold to increase the surface temperature to get close to the melt temperature to avoid or reduce the frozen layer. Then they apply a rapid cooling system with optimized cooling channel design and in some cases using an expanding gas for cooling.
Not only injection mold temperature determines melt temperature as it moves quickly through the mold. The melt temperature itself as it starts its journey through the injection mold (self-evidently) is the reference point. Speed of injection, particularly in thin sections, is of huge influence, as it will determine the degree of shear heating. Fighting against this will be the loss of heat to the injection mold. Forget the idea of notional mold temperature. In other words, it is a fantasy to imagine that coolant (water usually) set temperature is what the material encounters at each point in its journey.
It is a cyclically fluctuating parameter with each injection cycle and will vary from point-to-point over the entire pair of injection mold surfaces. This is why mold-filling and cooling simulation is such a great tool and does give a fantastically useful insight into what actually happens throughout each cycle. Only by measuring at/near injection mold surfaces dynamically (thermocouple) can anyone know what the REAL (not SET) conditions are actually being encountered by the highly compressible fluid we know as plastic. It never ceases to fascinate me.
It is a cyclically fluctuating parameter with each injection cycle and will vary from point-to-point over the entire pair of injection mold surfaces. This is why mold-filling and cooling simulation is such a great tool and does give a fantastically useful insight into what actually happens throughout each cycle. Only by measuring at/near injection mold surfaces dynamically (thermocouple) can anyone know what the REAL (not SET) conditions are actually being encountered by the highly compressible fluid we know as plastic. It never ceases to fascinate me.
The reduction of wall section should always be a "given" in any half-decent designer's approach to designing a component. Sometimes, however, the thinnest wall section that can be contemplated to fulfill key requirements are still what most would call "thick." I'm dealing with components at the moment (not injection molded, but thermoplastic) that are needed to withstand 40 tones short-term loading. Some ABS injection moldings I was aware of in the '80s were around 25mm thick (spin-welded fishing net flotation spheres) and — I am told — some modern fighter jet cockpit canopies are injection molded in polycarbonate at around 65mm!
Moldflow has been around for a third of a century and even in its first decade, I commissioned its use, in the hands of an expert and highly experienced injection mold designer to solve a molding problem that had jeopardized the main assembly line of a world-renowned automotive supplier. The injection mold in question had indeed been designed by highly experienced specialists, but they got it spectacularly wrong. The problem was simulated, tool modifications proposed and re-simulated, with promising results. The injection mold was physically modified in line with the simulated changes and immediately ran with effectively zero defects. Previously, convoys of taxis had to be reserved to ferry parts a round trip of over 800 km, just to keep the main line supplied with reduced numbers, as there had been at least 30% reject levels pre-modification. Now, THAT really was some experience!
Short Shot is a customer concern or symptom, and root cause could be one of many or combination of other process parameters. I have been out of injection molding for few years, but recall a DOE (design of experiment) completed in late 1990's to resolve the same issue. It could be mold temperature, injection pressure, barrel temperature, inconsistent cycle time (manual part removal).
Based on cavity pressure you will detect every short shot produced and will be able to sort out the respective parts as well. Additionally your people after a very short period of time will understand what they are doing and how to establish a stable process within a very short time. Have in mind your machine is not reliable as well as your operators are not. Cavity pressure monitoring will show you what an opened window or a changed injection speed, or a defective heater band for your quality produced means. So give them a try and you will learn a lot.
Based on cavity pressure you will detect every short shot produced and will be able to sort out the respective parts as well. Additionally your people after a very short period of time will understand what they are doing and how to establish a stable process within a very short time. Have in mind your machine is not reliable as well as your operators are not. Cavity pressure monitoring will show you what an opened window or a changed injection speed, or a defective heater band for your quality produced means. So give them a try and you will learn a lot.
As an engineering and manufacturing company in the China specializing in plastic injection tooling and molding we have been battling what we call 'purchaser apathy' ever since low labor cost countries entered the market in the 80/90's.
It has been too easy for the manager with the sign-off to pick the 'cheapest' quote without understanding what quality of engineering, tooling manufacture and partnership he is getting. The specifics of what we do does not lie now in actually 'cutting metal' this is largely computer controlled as "metal is metal" it is the service experienced before and after that adds the value.
What we find our customer value is us telling them no they can't do that because if they do it will impact total product quality or yes they can have an extra rib for strength in there but it will create a weld line right through their bose where the insert is going. Also find a company that has actual manufacturing on site as we do because it automatically aligns the customer and supplier goals (to make the tool as quickly as possible without compromising quality) why? Well because that's what we have here and if we quote a customer for tooling we must make it work and work to the best of it's ability for it to be a profitable and sustainable project.
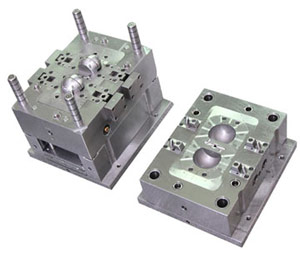
What we find our customer value is us telling them no they can't do that because if they do it will impact total product quality or yes they can have an extra rib for strength in there but it will create a weld line right through their bose where the insert is going. Also find a company that has actual manufacturing on site as we do because it automatically aligns the customer and supplier goals (to make the tool as quickly as possible without compromising quality) why? Well because that's what we have here and if we quote a customer for tooling we must make it work and work to the best of it's ability for it to be a profitable and sustainable project.
Impact additives add strength but also add cost, and may reduce stiffness (rigidity) which will be important during stacking. The injection mold is built so you aren't going to change the dimensions. The key then is cycle time -- relates to available machine hours, your accounting system, financing and things like that. There is little virtue in running faster if you're not selling out the machine time.
There are plenty of lower-MFI grades that are stronger, but they will mold slower, even at higher melt temps and injection mold temps. What is the real cost of running more slowly? If the products are cracking in service, the current cycle time is not a goal but a wish. HDPEs for pipe, milk bottles, bags and the well-known (in USA) post office tote boxes are made from fractional-melt grades, but you may not have to go that low. If you do use these, beware creating flow-line weaknesses which will encourage cracks in some places and not others, based on mold design.
There are plenty of lower-MFI grades that are stronger, but they will mold slower, even at higher melt temps and injection mold temps. What is the real cost of running more slowly? If the products are cracking in service, the current cycle time is not a goal but a wish. HDPEs for pipe, milk bottles, bags and the well-known (in USA) post office tote boxes are made from fractional-melt grades, but you may not have to go that low. If you do use these, beware creating flow-line weaknesses which will encourage cracks in some places and not others, based on mold design.
Regarding Continuous Compression Molding of plastic caps and containers, while talking about "compression" in general I'd be talking out of school. Continuous compression molding is a continuous extrusion process where the extruded plastic is cut in small gobs ("dose" o "pellet"), delivered into a cavity of a rotary machine (not index machine, it is a continuous rotary machine) and molded to the final shape.
This technology is extremely efficient time wise and energy wise and the parts produced are very consistent.
The plastic (HDPE or PP) is extruded at lower temperature than injection molding since there is no need to pump it through the hot runners and through the gate valves into the cavities. That saves power when melting the plastic and when cooling the part. Moreover colder parts means better dimensional consistency because you leave less to out-of-the-mold uncontrolled shrinkage.
This technology is extremely efficient time wise and energy wise and the parts produced are very consistent.
The plastic (HDPE or PP) is extruded at lower temperature than injection molding since there is no need to pump it through the hot runners and through the gate valves into the cavities. That saves power when melting the plastic and when cooling the part. Moreover colder parts means better dimensional consistency because you leave less to out-of-the-mold uncontrolled shrinkage.
In most cases injection mold shop will end up making "acceptable" parts by "shrink fixing" it. There goes all profit and residual stress is introduced.
I am asking Chinese mold flow experts- have you produced mold flow simulations with tools where either part thickness varies and or cooling channels are not uniform, or are not conformal with uniform pitch- how do you model uneven tool temperatures and uneven part thickness average temperature? Would you deliver a mold flow simulation with differential mold shrinkage so tool can be cut with compensation? Otherwise we are back to surrogate tool or prototype too?
On prototype mold worth remembering the tool material and cooling geometry can have vast difference in shrinkage and be disaster when proceeding to production tool from Al tool with minimal cooling.
I am asking Chinese mold flow experts- have you produced mold flow simulations with tools where either part thickness varies and or cooling channels are not uniform, or are not conformal with uniform pitch- how do you model uneven tool temperatures and uneven part thickness average temperature? Would you deliver a mold flow simulation with differential mold shrinkage so tool can be cut with compensation? Otherwise we are back to surrogate tool or prototype too?
On prototype mold worth remembering the tool material and cooling geometry can have vast difference in shrinkage and be disaster when proceeding to production tool from Al tool with minimal cooling.
I work for an OEM company, and we generally prefer United States injection molds for the following reasons. We have China injection molds in production now, but some of our experiences tend to make us prefer to keep tooling stateside.
- Mold Design - We tend to get better designed molds in the USA. If the injection mold can be designed in the US and build in China, this has produced superior molds for us.
- Lead Times - Maybe we just had a bad experience, but one injection mold seemed to take the slow boat across the ocean. The lead time wasn't competitive with a stateside mold.
- Mold Trial - Generally not possible to be on hand for the initial injection mold trial in China.
- Mold Modifications - We have gotten better/faster injection mold modifications when the mold was able to be sent back to the original mold maker in the USA. Sending the mold to China to be modified is cost prohibitive, so a 3rd party mold maker has to make the injection mold modifications.
I have traveled worldwide to many molding facilities in US, UK, Europe and China and found that it is quite common for cooling channels in injection molds to be clogged with various mineral deposits that accumulate over short periods of time. In some cases over a few weeks. This of course is a function of local water quality and whatever secondary filtering and/or water treatment that is at the injection molding factory. As you can imagine, the cleaning out of these mineral deposits can be very troublesome and typically requires the use of acids that are indeed risky to use on high quality precision tooling. It is a rather simple process to test for the increased % of flow restriction and may be a more valuable parameter to be used to verify cooling efficiency if indeed you are seeing variations in your parts that appear to be cooling related.